Post-Combustion CO₂ Capture Add-on for Power Plants – solid fuels
In this factsheet a generic end-of-pipe solution to capture CO2 from flue gases after the combustion of solid fuels such as coal, solid biomass and municipal solid waste (MSW) in power plants is considered. Similar technology can be used for large boilers, but these are not the focus of the factsheet. Reference plants are solid fuel power plants without CCS ((ultra)supercritical coal/lignite, solid biomass, MSW, etc.).
Downloads
Download hier de datasheet (PDF)There are different requirements for flue gas cleaning and preparation for CO2 capture (dust filters, NOx removal, sulphur scrubbers, etc.) which will influence performance and costs. The performance and cost ranges are considered to be sufficiently close for the variety of solid fuels to group them together in a single factsheet.
Post-combustion capture can be attached to an existing power plant or incorporated in the design of a new plant, the latter with potential for increased efficiency and lower total costs. The focus of this factsheet is add-on capture for a stand-alone plant, regardless of age or type of solid fuel, and therefore does not take into account potential efficiency gains or cost reductions from integrated design of new plants.
Post-combustion CCS generally entails capture from flue gases with low CO2 concentrations. In the case of solid fuels CO2 concentrations are generally below 15% (IPCC, 2005; IEAGHG 2013). There are a variety of techniques that can be used to separate CO2 from the flue gas, including using sorbents/solvents, membranes and distillation machinery. Chemical solvents, such as Mono-Ethanolamine (MEA), are the most commonplace technique for post-combustion capture for power plants (IPCC 2005), therefore they are considered the default for this factsheet. After CO2 capture, a regeneration step is required to release the CO2 and clean the solvent so it can be reused.
By adopting amine technology, 85-95% of CO2 can be captured from the flue gas (IPCC, 2005). Energy requirements for capture and compression of CO2 lead to higher fuel consumption, hence net CO2 reductions achieved are lower than the capture rate. CO2 emission reduction rates for coal power plant retrofits range from 63%-94%, depending on whether emissions from auxilliary energy supply are captured or not (IPCC, 2005; Rubin et al., 2015a, Mantripragada, 2019).
Compression and dehydration of CO2 is part of the capture process. CO2 pressure after capture varies from 8 MPa to 20 MPa in the studies cited here. At these pressure levels it is possible to transport the CO2 through low-pressure pipelines (maximum pressure of 4.8 MPa) or high-pressure pipelines (minimum of 9.6 MPa) (IPCC 2005) with minimal additional (de)compression required. It is therefore assumed that no additional compression step is required after capture to prepare the CO2 for pipeline transport. If CO2 is transported in liquid state, then additional compression will be required.
All information in the datasheets is also available in ESDL (Energy System Discription Language). You can find them in the Energy Data Repository (EDR).Gerelateerde publicaties
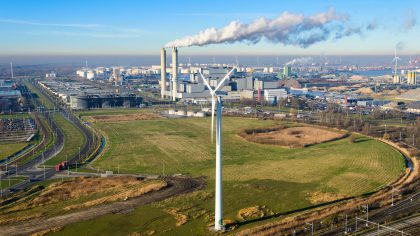
Toename aandeel hernieuwbare warmte
Haalbaarheid van de RED III-doelstellingen met het huidige beleid
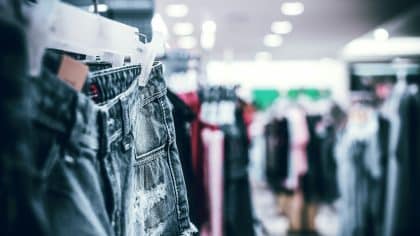
Communicatie over klimaatbeleid
Vergroot waardegerichte communicatie het draagvlak voor een toeslag op fast-fashion?
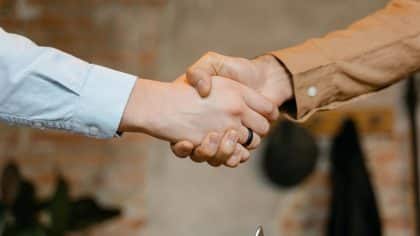
Implementatie van energiedelen
Energy sharing: a new activity for active customers and energy communities