All information in the datasheets is also available in ESDL (Energy System Description Language). You can find them in the Energy Data Repository (EDR).
Coal-fired power plant (Co-firing biomass) – electricity production and district heating
Working of the Technology
A coal-fired power plant can be a combined heat and power plant (CHP). The fuel input consist of pulverized coal. In some cases biomass is cofired. Water is evaporated in a boiler to produce high pressure steam which is expanded in a turbine to generate electricity using a generator. Residual heat is cooled down by using a cooling technique, for instance cooling towers. From the drain of a steam turbine heat can be fed into a district heating network. Heat can be supplied to different sectors such as the built environment or industry. This factsheet focuses on a CHP plant that delivers heat to the built environment. A CHP plant without carbon capture and storage (CCS) is considered in this factsheet.
Main components
Components of a coal-fired power plant for the production of electricity and district heating typically consist of fuel storage/fuel feed, steam boiler, economiser/heat exchanger (i.e. feedwater heaters; commonly used as part of a heat recovery steam generator in a combined cycle power plant), turbine and generator, cooling technique, flue gas cleaning equipment and ash conveyor.
Energy production related aspects
The downside of utilizing heat for district heating is that the electrical efficiency of the CHP plant is lowered (loss of electricity production) (ECN, 2011). Loss of electricity production (GJe/GJth supplied) depend on the temperature of heat disconnection. Typical losses are included in this factsheet.
Coal-fired CHP plants are equipped with flue gas cleaners to limit/prevent emissions of various harmful substances (such as particulate matter, NOx, SOx). The flue gas cleaner is included in the costs presented in this factsheet.
Downloads
Coal-fired power plant (co-firing biomass) - electricity production and district heatingGerelateerde publicaties
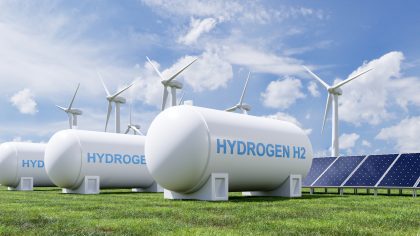
Effecten van waterstofimport op de industrie in Nederland
Exploration of the effects of (partially) replacing Dutch fertiliser and iron and steel production with imports

De weg naar toekomstbestendige petrochemie
Exploration of transition strategies in Dutch refineries and organic chemicals industry for climate policy
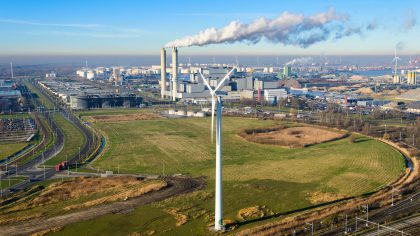
Toename aandeel hernieuwbare warmte
Haalbaarheid van de RED III-doelstellingen met het huidige beleid